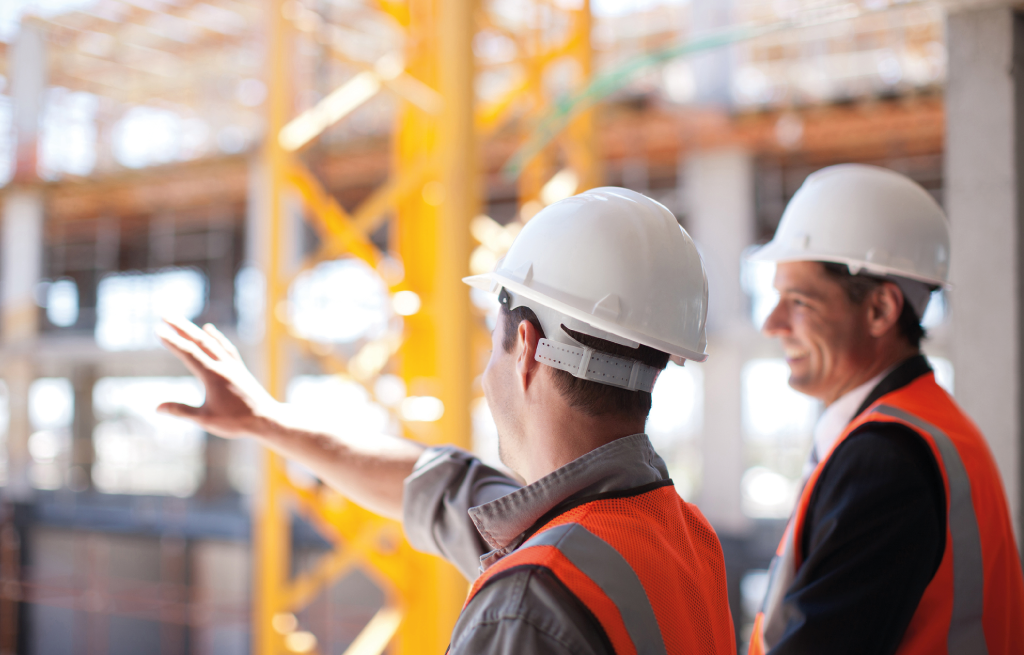
LOCKOUT TAGOUT (LOTO) AND THE MOVE TO LOCKOUT, TAGOUT, TRY-OUT (LOTOTO)
Working on industrial equipment and machinery can be incredibly dangerous and each year thousands of workers get injured, sometimes fatally, whilst performing basic maintenance and repairs. A lot of these accidents occur as a result of the uncontrolled release of energy, which exists in many forms. Due to the uncontrollable and unpredictable nature of energy, OSHA Regulations require that all energy sources be isolated and ‘locked out’ whilst services and repairs take place.
Read our guide below for more information on Lockout Tagout
- What is Lockout Tagout?
- Why use a Lockout Tagout strategy?
- Types of Energy
- 9 Step Isolation Procedure
- Setting up a Lockout Tagout Strategy
- FAQs
WHAT IS LOCKOUT TAGOUT?
Lockout Tagout (LOTO) procedures ensure that the hazardous energy sources are isolated and rendered inoperable before any maintenance work commences. A safety lock is used when the energy source is turned off to prevent it being switched on. Locking out refers to the physical method of isolating a piece of equipment or machinery to prevent it from releasing stored energy or potentially re-energising whilst work is being done on it. Tagout specifically refers to the visible written warning, on an attached tag or sign, that a piece of equipment is locked out and should therefore not be used. It should be highly visible and obvious.
LOTOTO increasingly is being used to highlight the activity of attempting the re-energisation of the locked out equipment to check that all is in order – prior to starting the work. LOTOTO describes the Lockout, Tagout, Try-out steps where the formal addition would identify if there were any faults with the Isolation Point(s) where further work would be needed to address these prior to any planned work commencing. A good example of this is a faulty rotary electrical isolator – it could be easily turned off and lockout out but remaining energised due to a common mechanical breakage of the isolator internals.
WHY USE A LOCKOUT TAGOUT STRATEGY?
Having a lockout tagout strategy in place in your business helps to severely reduce the risks involved with working on equipment. It puts in place a System of Safe Working which helps to ensure the safety of all workers and reduces any risk of employer’s being liable to prosecution should any accidents occur as the HSE would expect such systems exist. In addition to the obvious safety benefits, having a lockout tagout strategy can help reduce unplanned downtime and thus increase productivity in the workforce. A food or chemicals plant would suffer major contamination wastage if a valve were to be closed accidentally – lockout can also be used to “lock on”.
TYPES OF ENERGY
There are many different types of energy which can be potentially dangerous to workers whilst repairs and maintenance are performed on equipment. Some of the main types of energy which are potentially hazardous in the workplace are;
Electrical
Electrical energy is one of the most common types of energy, is found in nearly all workplace equipment and often the one given, probably incorrectly, the single focus to LOTOTO. The obvious hazard is that it will re-start the equipment which will introduce major risk of injury.
Chemical
Chemical energy refers to the energy associated with chemical reactions; such as synthesis or decomposition. Primarily the risks associated with chemical energy include uncontrolled reactions, fires, burns and explosions.
Thermal
Thermal energy is often present in steam and hot water systems where processes require or produce such things. Severe injuries are obviously highly likely through direct accidental contact to these but a pressurised steam vessel has enormous energy to be considered and isolated correctly.
Kinetic
Kinetic energy refers to energy of machinery or equipment due to motion; for example, rotating flywheels and belts. Electrically isolating a machine is instant but the removal of kinetic energy takes further efforts and older equipment may not have the same braking systems as newer equipment. The general risks come from being caught in, caught on or caught between equipment moving as a result of stored kinetic energy.
Potential
Potential energy is similar to kinetic energy and refers to the moving parts of machinery. The risks associated with potential energy are more around the storage of energy following movement such as a bucket loaded with rocks on a conveyor where the potential energy may force the movement despite the electrical isolation.
Pneumatic
Pneumatic energy is most likely found powering machinery via compressed air or gas. The hazards associated with pneumatic energy start with the destructive potential of a high-pressure air escape through to the sudden movement of mechanical equipment due to an unreleased pressurised air system.
Hydraulic
Hydraulic energy is used to power forklifts, cutting equipment and pumps. Where pneumatic energy powers via air and gas; hydraulic energy powers via high-pressure fluid. An escape of hot hydraulic oil through a valve will do serious harm to the unfortunate recipient whilst sudden or slow movement of the mechanical equipment through stored hydraulic pressure carries huge force due to the non-compressible nature of the fluid.
9 STEP ISOLATION PROCEDURE
Generally, each piece of equipment could need locking out in different manner however there are a variety of general steps to an isolation. Performing a lock out tagout audit of your workplace will help you identify a specific isolation procedure for your equipment. Isolation refers to the blocking of all energy sources.
Preparation
Before any equipment is shut down the responsible person will review the works order and possibly give a briefing to their direct team performing the work with the equipment and lockout process. They must consider the type and amount of energy that powers the equipment or is created by it, the hazards it creates and how it can be controlled. Any Safe Working Practice will have a risk assessment that must be reviewed as part of this step. Often a record must be completed – from a simple lockout register up to a full Permit to Work
Notify
The responsible person MUST notify ALL affected individuals via radio, physical entry or the control room. This may require additional demarcation notification such as barrier tape or physical temporary barriers.
Turn Off/Shutdown
The equipment is shut down as per the normal procedure specified by the company which, in turn, will follow the manufacturers guidelines. The shut down is in a methodical manner to avoid adding hazards arising from an emergency stop.
Isolation
Isolation points should be clearly identified in procedures and labelled. Then, install energy isolation devices which will block the equipment from the energy source. Make sure you isolate all the energy sources and secondary supplies. Make sure you don’t just remove the fuse; this isn’t the same as isolating the device. Visually check that the isolation is successful in stopping moving equipment and, where visible, contactors have parted. Finally, check that access to the work area remains restricted and access points have not been inadvertently created during the previous steps.
Lockout and Tagout
In accordance with your company’s procedures, energy isolation devices should be locked out and tagged. Make sure only devices supplied by the employer are used. Plant locks must be applied with an appropriate multi-hasp and this will then have personal locks applied for each person involved in the job.
For larger jobs a lockout box may be needed to ensure the responsible person has control over a large number of padlocks and keys. Ideally a personal lock should be fitted with an appropriate safe isolation warning tag.
If it is not possible to lock out an energy source then an alternative method and information tag must be applied as a means of protection. Fuses can be removed, air pipes removed, lines bled, rooms locked, valve handles fixed with chain etc. Even though it may not be as convenient as switching off an isolator these additional actions could save a life. Any tag can only be removed by the applying responsible person and it should be considered an offence to bypass, ignore or forcibly remove for convenience.
Controlling the Zero Energy State
You must ensure that you guard against energy left in the equipment and inspect to make sure all parts have stopped moving. Make sure to release the tension on springs or block their movement. Also block parts which could fall due to gravity (potential energy) and do the same for parts in pneumatic and hydraulic systems which could move from a loss of pressure.
Make sure to drain process piping systems, close valves and bleed lines and leave vent valves open. Make sure to relieve trapped pressure and purge reactor tanks and process lines. Make sure energy cannot re-accumulate as in the case of air systems.
Try out - Isolation Verification
Make sure the hazardous area is clear of all personnel and verify that the main disconnect switch or circuit breaker cannot be switched on. Use a voltmeter or similar to check the switch and attempt to start the equipment; then shut off all machine controls when testing is finished. If a fault is spotted at this stage it is essential that all work stops and the fault is addressed – it is too tempting to work around it on the basis that others know.
Performing the Work
Complete the planned work as per the risk assessment and avoid doing anything different which could accidentally re-activate the equipment and never bypass the lockout when putting in new piping or wiring. If, at any point, it is suspected that an energy source now exists stop the work immediately, report the incident and investigate when authorized to do so.
Inspect and Restore
Visually inspect the area and check that any removed guarding is back in place securely. Make sure the responsible person removes the final lock and energize the equipment based on company procedure before notifying all employees that the equipment is ready to use. Never allow anybody to remove someone’s personal lock. All devices should be restored to their operating position and verify it is operating correctly.
SETTING UP A LOCKOUT TAGOUT STRATEGY
It is important to have a lockout tagout strategy within your business as it makes for a safer workplace and will detail all necessary steps to safely isolating equipment. There are a few steps involved in setting up a successful strategy.
- Appraisal of Equipment - The first step in creating a successful strategy is identifying all the equipment which requires energy isolation during maintenance, cleaning and repair. Make sure for each piece of equipment there is plenty of detail about the associated energies, isolation points and sequence of isolation. Make sure to consider environmental factors also such as confined spaces and other safety factors associated with each piece of equipment. Each isolation point should then be identified with a unique code that is then shown at the isolation point by a tag or label.
- Procedures - Review your appraisal to begin to develop equipment specific procedures; you can identify lock out tagout product requirements during this phase also. Procedures should then be posted alongside the equipment and an “isolation map” is a good practice to use here to make the process simple.
- Policy and Plan - Now procedures are in place, a written policy for lockout tagout can be prepared. It should describe all processes required in order to successfully control hazardous energy. It should include things such as responsibilities, training, isolation, lockout tagout and permits to work. Be careful that all standards refer to the OSHA Regulations. Refer to OSHA 1910.147 for the Lockout Standards.
- Training - All those who need to be involved with the strategy need appropriate LOTO training and access to the relevant lockout tagout products. The policy and procedures need to be integrated into this training and this must include a competence assessment with a pass/fail method as evidence. Further down the line it is vital to train new staff on the policy and procedures also. Any changes to the plant must be reflected in the training delivered as well as the procedures – the latter is a common failing in modern businesses undergoing regular change through capex and CI.
- Implementation - Now it is time to implement the strategy, make sure members of the leadership team are all on board and prepared to motivate the team to implement this new strategy. Regular reviews and audits are also key to ensuring the process is running smoothly and safely. Remember it is often the cleaners, contractors and management that are overlooked when implementing a Safe System of Work with LOTOTO.
FAQ’S
Why do I need a Lockout Tagout Strategy?
Having a lockout tagout strategy in place helps to keep your employees safe whilst performing repairs and maintenance on equipment. An uncontrolled release of energy is extremely dangerous and can cause serious injuries and death if handled incorrectly. Telling quote recently from an HSE Inspector summed it up: “We are not having to create new ways of killing people!” Failure to safely isolate energy sources is still a major contributor to industrial fatalities and also ranked 6th in OSHA's list of workplace safety violations in 2022.
How do I implement a strategy in the workplace?
There are several steps to implementing a successful lock out tagout strategy in the workplace but begin by appraising all your equipment so you can understand your lock out needs and go from there.
What are the dangers associated with Energy?
Each energy source produces their own hazards but for example when it comes to the most common energy source; electrical, the dangers mainly stem from an unexpected starting of the moving machinery arising from incorrect lockout or faulty isolators.
What lockout equipment do I need?
The type of lockout equipment you need will depend on the equipment or machinery you plan to lockout. When setting up your strategy you’ll need to assess the individual requirements of each piece of equipment and choose lockout products based on this. If there are multiple isolation points you need to have a simple and robust complex isolation system (group lockout) in place.